Fossil-Free Sponge Iron for the Steel Industry: Receives SEK 3 Billion for Plants in Northern Sweden
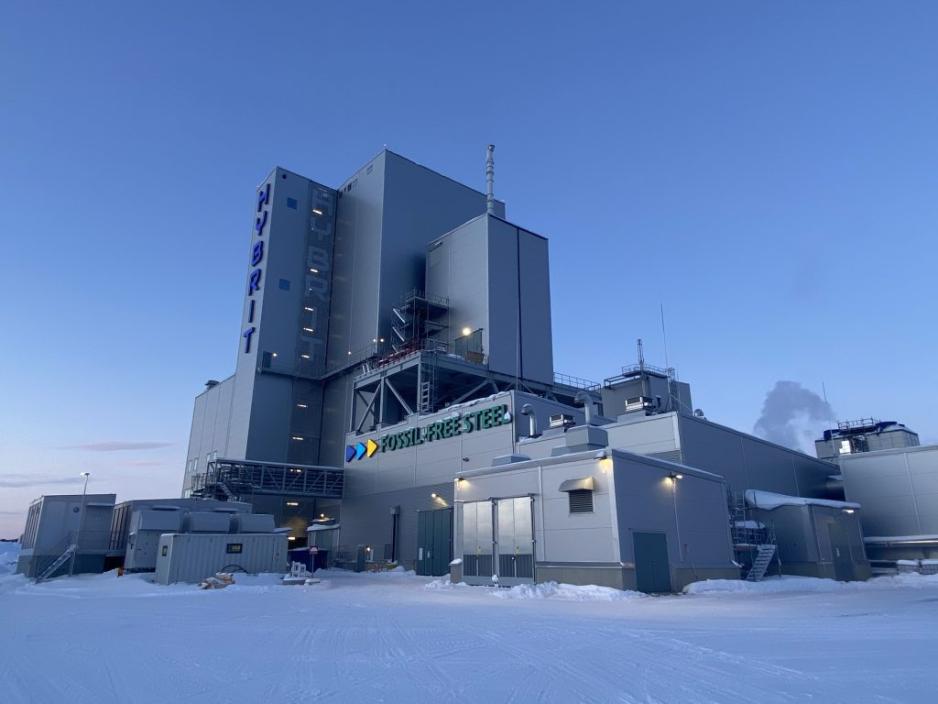
The photo shows Hybrit's pilot factory for test production of sponge iron in Luleå. The three billion will go toward the plant to be built in Gällivare in Northern Sweden. Here, fossil-free sponge iron will be produced, which is used in the production of fossil-free steel. (Archive photo: Hybrit)
Mining company LKAB and the Hybrit project will receive SEK 3.1 billion from the Swedish Energy Agency. This will go towards building a demonstration plant in Gällivare, Northern Sweden, to produce fossil-free sponge iron for the steel industry. The facility has the potential to reduce Swedish CO2 emissions by approx. 1.8 million tonnes per year.
The Swedish Energy Agency grants a total of SEK 3.1 billion in support to LKAB and Hybrit Development AB through Industriklivet (the Industrial Leap).
This was revealed in a press release from the Energy Authority on Thursday.
Hybrit was initiated in 2016 by the three owners; SSAB (steel company), LKAB (mining company) and Vattenfall (energy company). With the partnership in Hybrit, the three companies will create a completely fossil-free value chain from mining to finished steel, with fossil-free pellets, fossil-free electricity, and hydrogen.
Fossil-free sponge iron for the steel industry
The companies LKAB and Hybrit Development AB are behind the application, which has now been approved, and the support will go toward establishing a demonstration facility for the so-called direct reduction of iron-ore, including hydrogen production.
The facility will be built on LKAB's existing industrial area in Gällivare in Northern Sweden. At full production, 1,35 million tonnes of fossil-free sponge iron will be produced per year.
"The processing and production of fossil-free sponge iron is central to the climate and to the Swedish competitiveness. We are pleased with the announcement that the state is participating and sharing the initial risk in this crucial step to industrialize the Hybrit technology. In order to counter climate change, we need to move forward quickly, and to keep up the pace, it is important that we get all the prerequisites in place for future investment decisions, " says Jan Moström, CEO of the state-owned mining company LKAB, in the press release.
The company operates several iron ore mines in Northern Sweden – and is investing greatly in the production and further processing of minerals and metals. LKAB is heavily involved in the transformation of the iron and steel industry, and the plan is to develop carbon-free processes and products within 2045.
"This is a huge opportunity for Sweden and for the climate. Our high-quality iron ore combined with good access to fossil-free energy gives us unique conditions compared to other countries to establish a sustainable and competitive value chain for the fossil-free iron and steel production of the future," Moström adds.
Can reduce large amounts of CO2 emissions
The Swedish Energy Agency points out that the Swedish iron and steel industry is an emissions-intensive industry, but also crucial for Swedish exports and the economy. Production of fossil-free steel from mine to finished product will strengthen Swedish competitiveness and, in the long term, European competitiveness, the press release states.
"The demonstration plant has the potential to reduce Swedish carbon dioxide emissions by approx. 1.8 million tonnes per year. That the technology will now be demonstrated on an industrial scale is important for the transition in the steel industry. The experiences will be able to be disseminated and used outside the project, says Klara Helstad, head of the unit for sustainable industry in the Energy Agency.
Facts about HYBRIT
The HYBRIT technology involves iron ore pellets being reduced to sponge iron with hydrogen instead of with coal and coke, which means that virtually all CO2 emissions are eliminated from iron and steel production.
The pilot plant for test production of sponge iron in Luleå, Northern Sweden, first started operating in 2020.
In 2021, Gällivare was chosen as the location for the planned demonstration plant for the production of fossil-free sponge iron on an industrial scale. Sponge iron is used to make steel in the next step.
In August 2021, SSAB produced the world's first fossil-free steel with HYBRIT technology and delivered it to customers.
The steel industry in the world currently accounts for 7 percent of total global carbon dioxide emissions. With the help of HYBRIT technology, SSAB can help reduce Sweden's carbon dioxide emissions by 10 percent and Finland's by 7 percent.
Major economic decision
The Swedish Energy Agency highlights that Sweden aims to be fossil-free within 2045 and then achieve negative emissions. The industry, responsible for a third of Sweden's fossil carbon dioxide emissions, must change its operations to reach this goal. They write that broad investments in innovative and untested but promising technologies are therefore necessary.
"The future competitiveness of the Swedish industry lies largely in becoming completely fossil-free. Therefore, the investments within the Industrial Leap are of great importance not only for climate and environmental reasons but also for access to expertise and employment in our country's new and old industrial sites. The decision we are now taking is the biggest financial decision that has been taken so far in this work, and it is important," says Robert Andrén, Director General of the Swedish Energy Agency.
The owner companies in Hybrit have contributed around 75 percent of the project's technology development funding. SSAB, LKAB, and Vattenfall have invested a third each, a total of approx. SEK 1.7 billion, in a feasibility study for the pilot phase, implementation of the pilot, and a feasibility study for the demonstration phase. HYBRIT has previously received over SEK 520 million in state aid.