Alcoa Mosjøen Makes Large-Scale Investment in the Green Shift
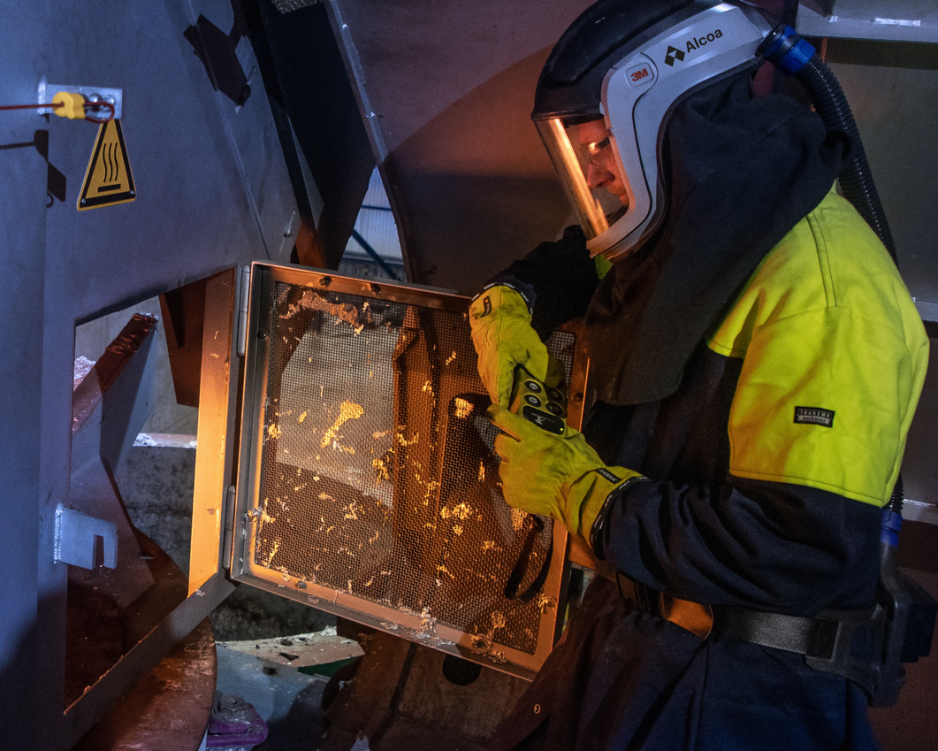
Operator Espen Breivik inspects the smelting process. Renewable electricity is sent into a coil where it encounters resistance. This leads to heat that smelts the aluminum completely emission-free. (Photo: Alcoa)
Alcoa Mosjøen’s new induction oven is to recycle aluminum waste only using renewable energy. The de-carbonization project will save annual emissions equaling those of 1,000 fossil fuel cars.
At the Alcoa aluminum plant in Mosjøen, Norway hundreds of millions of Norwegian kroner are put into green industry. The company recently announced that a new induction oven is now ready for use. It is to smelt and recycle aluminum waste completely emission free.
“The oven is to handle post-industrial waste metal, in other words; pure waste”, says Head of Communications Trym Solhaug Vassvik of Alcoa Norway to High North News.
“Imagine the process when you make lids to soda cans. You cut these out from a flat metal plate. It leaves large holes in that plate, yet the plate in and of itself is still valuable. What we then do is to roll it into a briquette and send it back to Mosjøen, where we put it into the induction oven”, he explains.
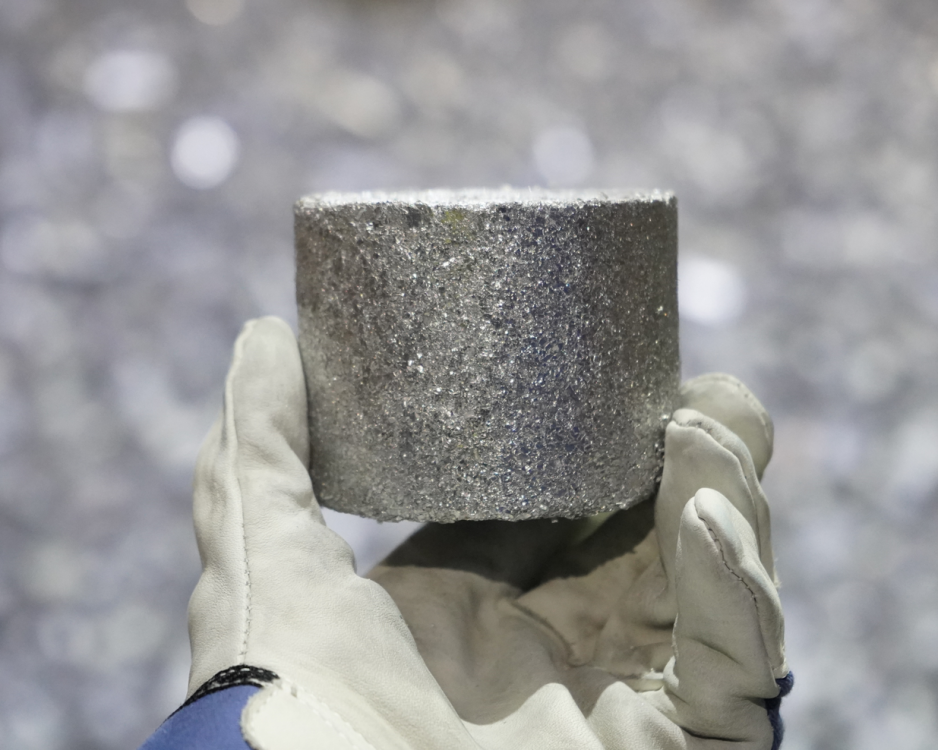
Pure aluminum waste has been compressed into briquettes and are ready for recycling. Aluminum is a sustainable metal with unlimited areas of use. It is something called closed-circuit-recyclable, meaning that it can be re-smelted time and again without losing its capacities. (Photo: Alcoa)
De-carbonization project
The process of exploiting aluminum waste has previously led to large emissions. The traditional way of doing this has been to use a cast oven heated on natural gas. The new Alcoa induction oven will use renewable energy from wind and water power. According to Alcoa, replacing natural gas with renewable energy will save Alcoa Mosjøen of some 4,400 metric tons of CO2 every year, equaling emissions from 1,000 fossil fuel cars.
Thus, the oven represents an important addition to the company’s aim of being fully carbon neutral by 2050.
In addition, some five percent of the energy is used to re-process waste rather than producing the similar amount of new primary aluminum, Alcoa says.
“The process is less energy intensive, and it is better for the environment that we exploit old waste rather than making new primary aluminum”, Vassvik says.
This demonstrates will to make an effort in Mosjøen and Northern Norway
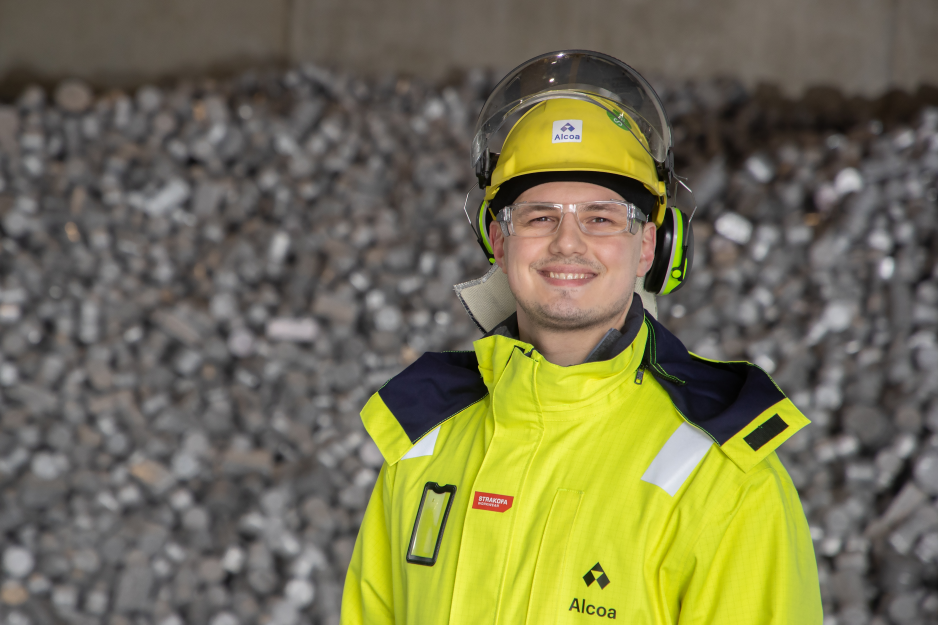
Trym Solhaug Vassvik, Head of Communications of Alcoa Norway. (Photo: Alcoa)
From waste to electric cars
The induction oven is a collaboration between Alcoa and the German metal dealer and Alcoa customer MMG. MMG will supply scrap metal in the form of aluminum alloys.
Alcoa Mosjøen will smelt the aluminum alloys, add primary aluminum depending on the customer’s specifications and return the metal to a.o. MMG and a new life cycle to everything from electric cars and bicycles to recycable cans.
The result is that Alcoa Norway can offer the world long-desired low-carbon aluminum, the company writes. The induction oven will provide the collaboration with an annual production of some 20,000 tons of low-carbon aluminum, however, there is a potential to increase production beyond this.
Head of Communications Vassvik says it is important that Norway produce more aluminum in a time when aluminum prices are high and the market is under pressure based on geopolitical conditions.
“We will have 20,000 tons more of low-carbon aluminum annually from Alcoa Mosjøen with this oven. That is not a giant amount, however, these amounts are in high demand”, he points out.
“It is important for this resource not to be wasted. Here, we really exploit the raw potential of aluminum. It is an indefinitely recyclable green metal, re-used in a green way through renewable energy and is through its capacities an important building stone for the Green Shift. This is the Green Shift put into practice”, says Plant Director of Alcoa Mosjøen Roy Hammer in a company press release.
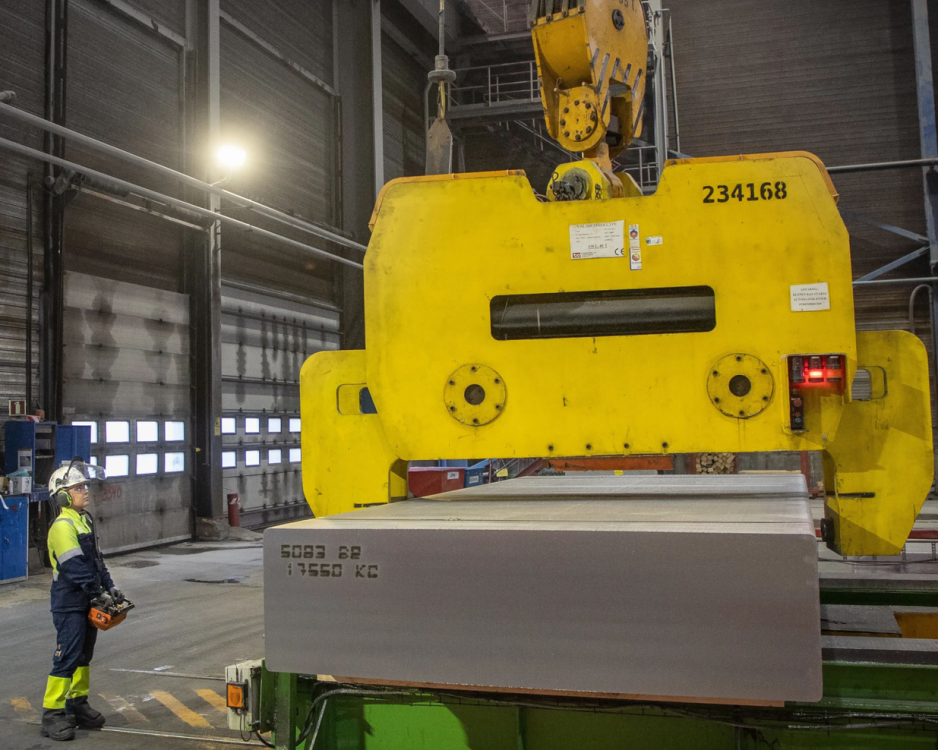
Casting operator Malin Salomonsen is in full control of the 17.5 tons heavy roller element containing recycled metal. The roller element is shipped to customers who make everything from soda cans to electric cars. (Photo: Alcoa)
New jobs
Alcoa Mosjøen is the northernmost aluminum plant of both Alcoa and of Norway. The global aluminum corporation headquarters are located in Pennsylvania, USA.
The new induction oven at Alcoa Mosjøen is the largest growth investment case of the global aluminum corporation through all of 2021.
Even though the induction oven is almost fully automated, it still needs some helping hands. 12 new full-time positions have been crated in relation to its operations, which leads to values and jobs in the local community, Alcoa says.
“This investment demonstrates a will to make an effort in Mosjøen and Northern Norway. There is a will to invest into industry and this is the Green Shift in practice, which allows us to take Alcoa into a green future. This creates jobs locally, values, and strengthens Alcoa’s company case. It is on a general basis an important addition to our operations, as it allows us the opportunity to produce low-carbon aluminum, a product increasingly in demand by the market due to people’s being conscious of climate change”, Head of Communications Vassvik says in closing.
New induction oven at Alcoa Mosjøen
Also read
This article was originally published in Norwegian and has been translated by HNN's Elisabeth Berqguist.